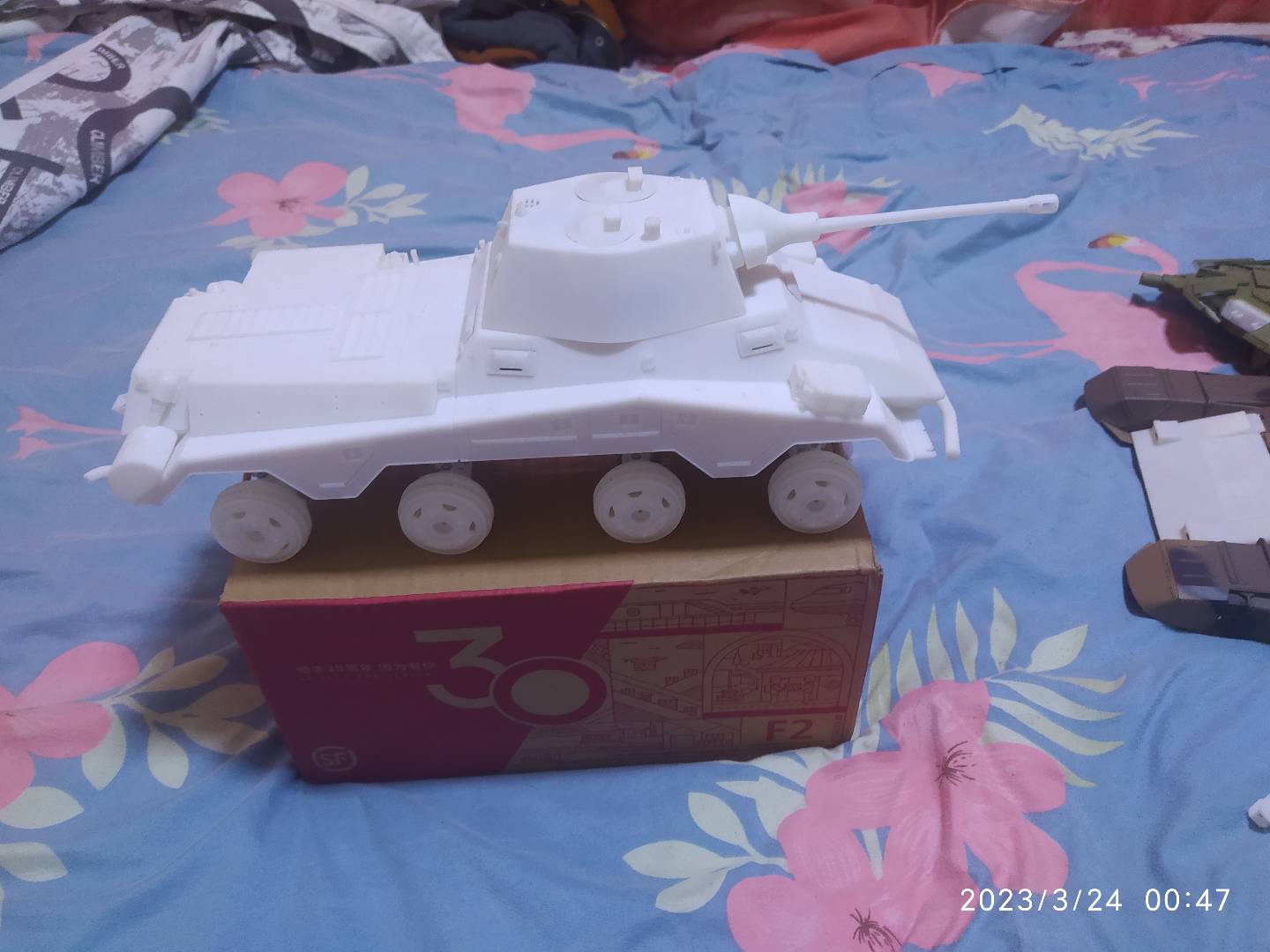
- IMG_20230324_004708.jpg (109.31 KiB) Viewed 1371 times
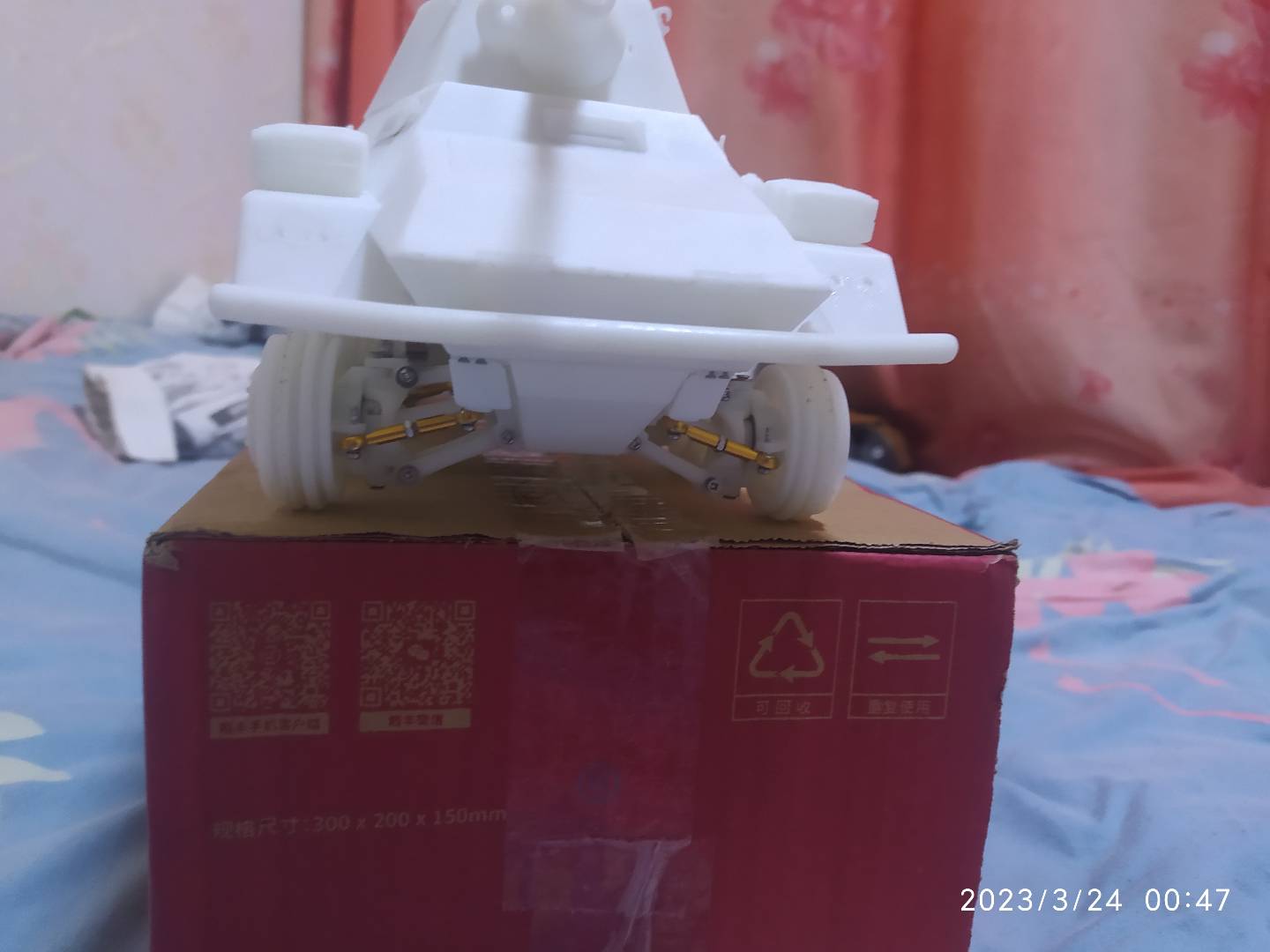
- IMG_20230324_004719.jpg (69.32 KiB) Viewed 1371 times
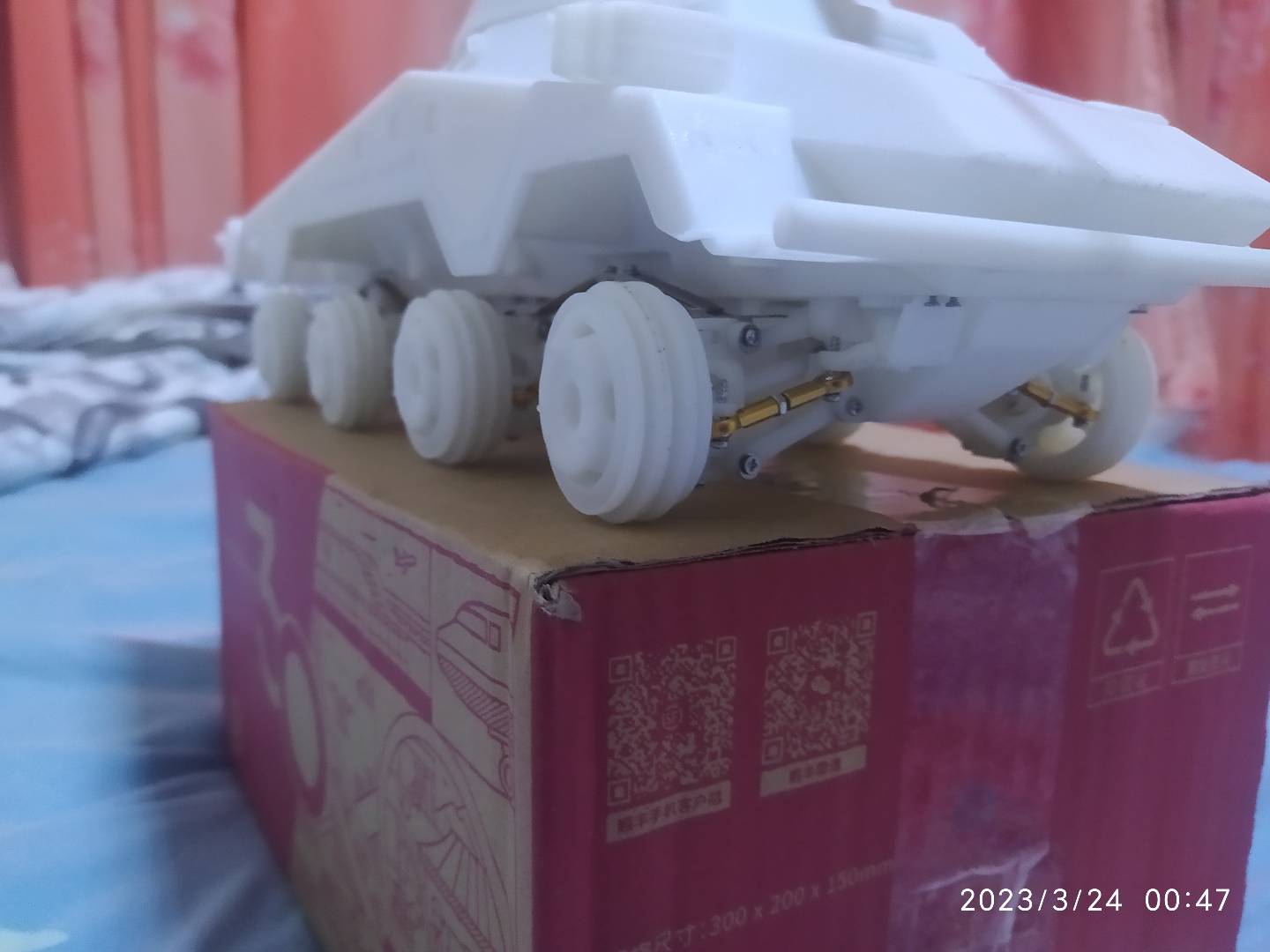
- IMG_20230324_004722.jpg (77.1 KiB) Viewed 1371 times
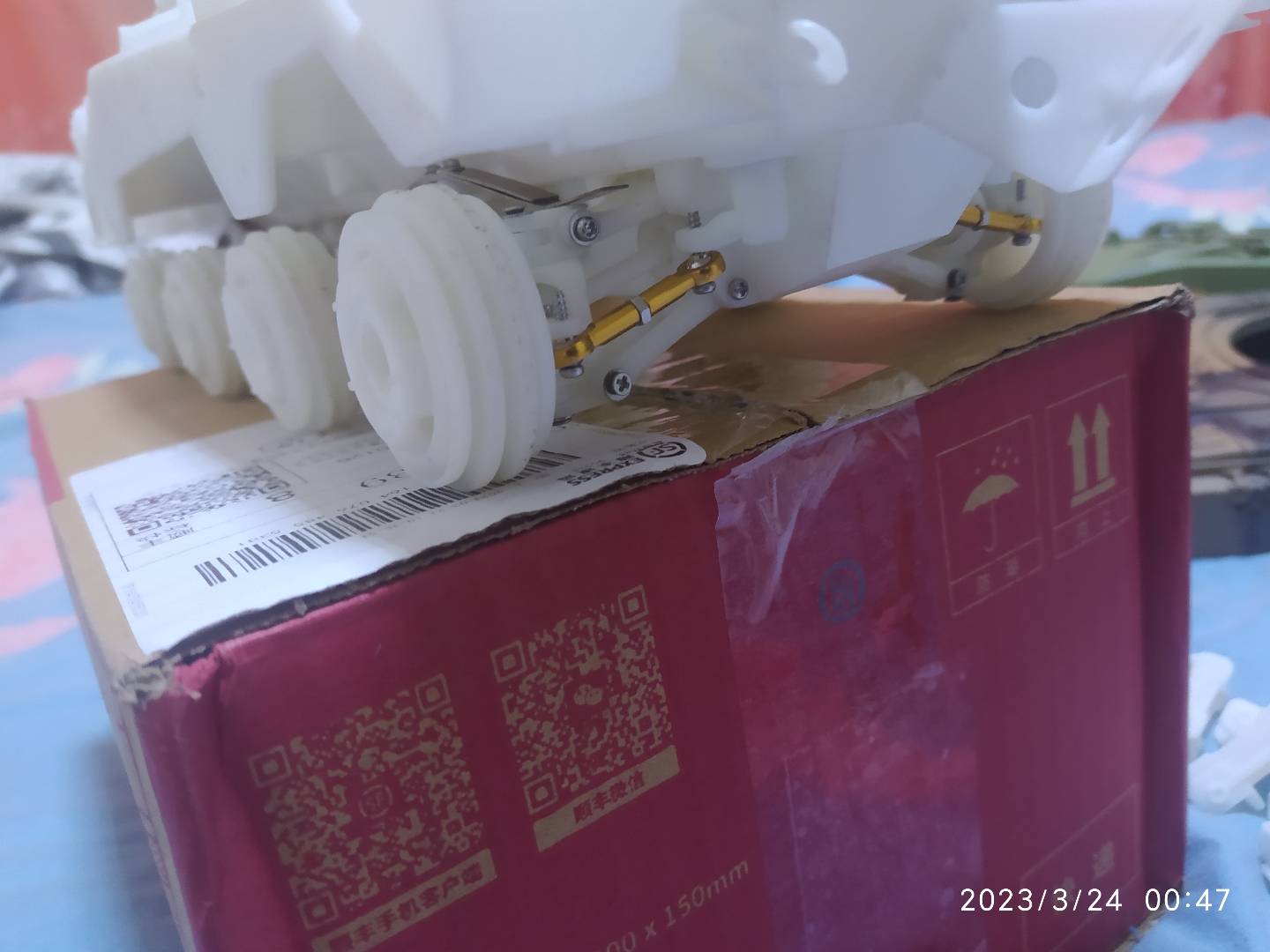
- IMG_20230324_004731.jpg (85.53 KiB) Viewed 1371 times
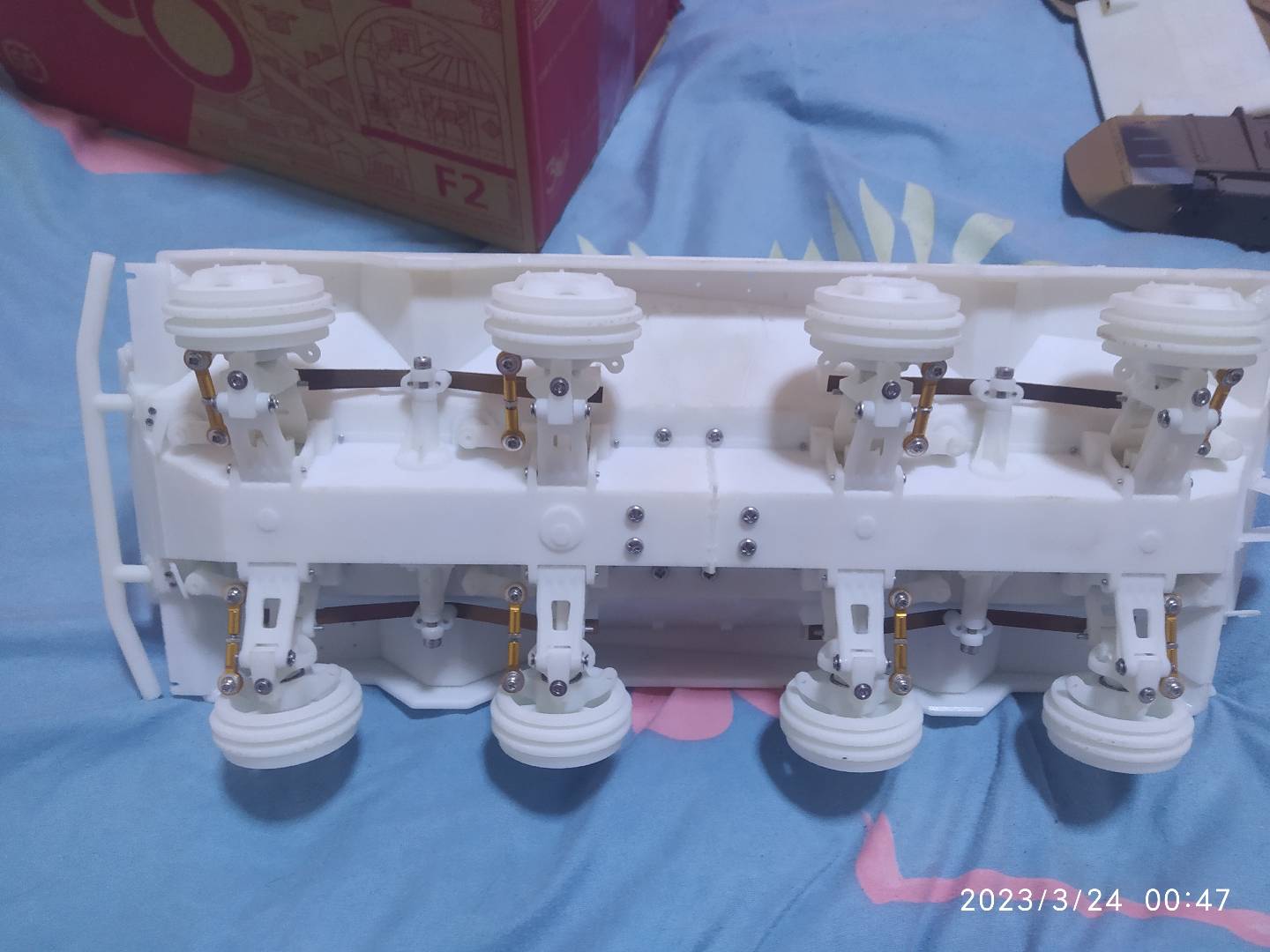
- IMG_20230324_004742.jpg (108.57 KiB) Viewed 1371 times
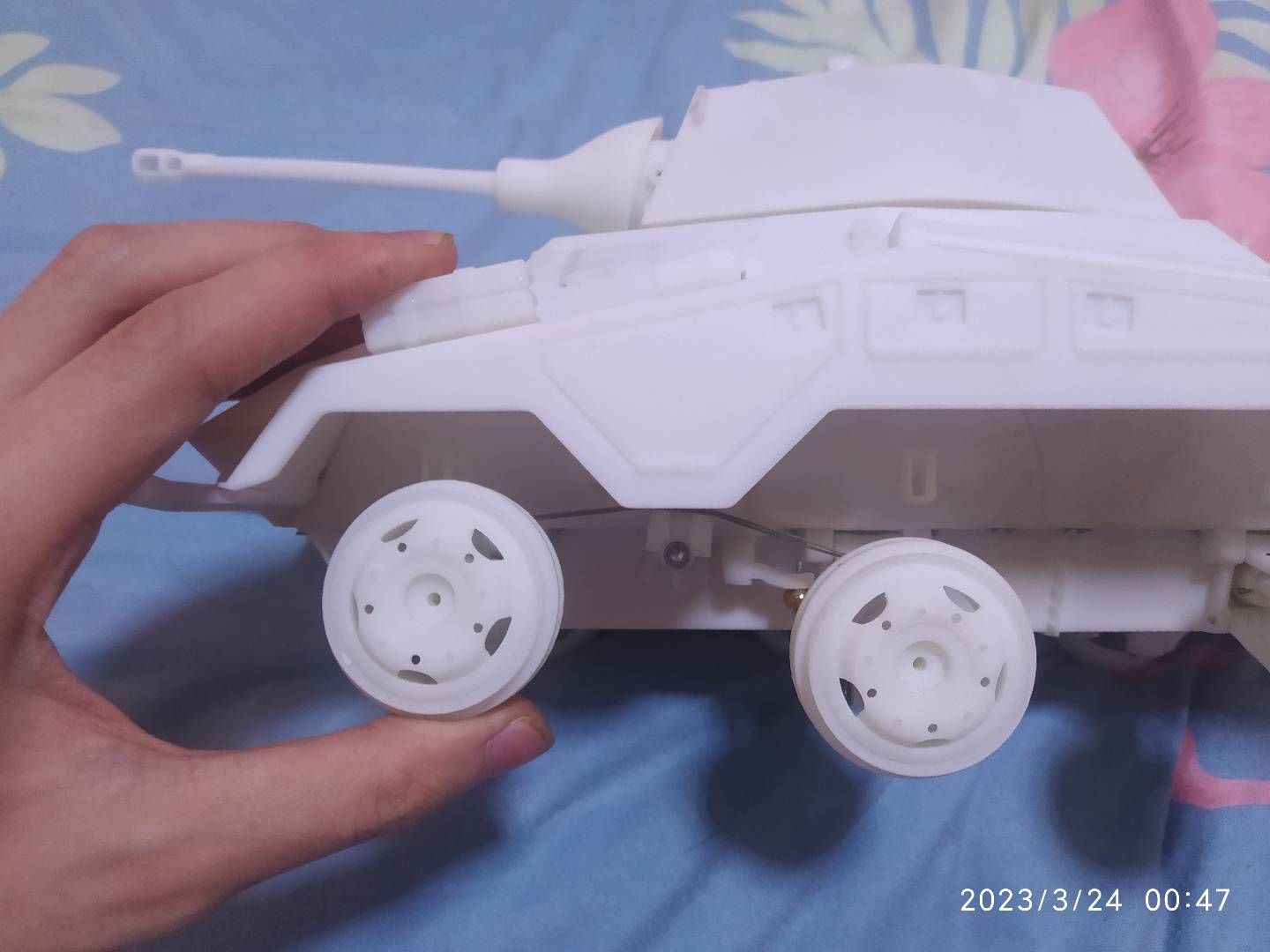
- IMG_20230324_004750.jpg (76.54 KiB) Viewed 1371 times
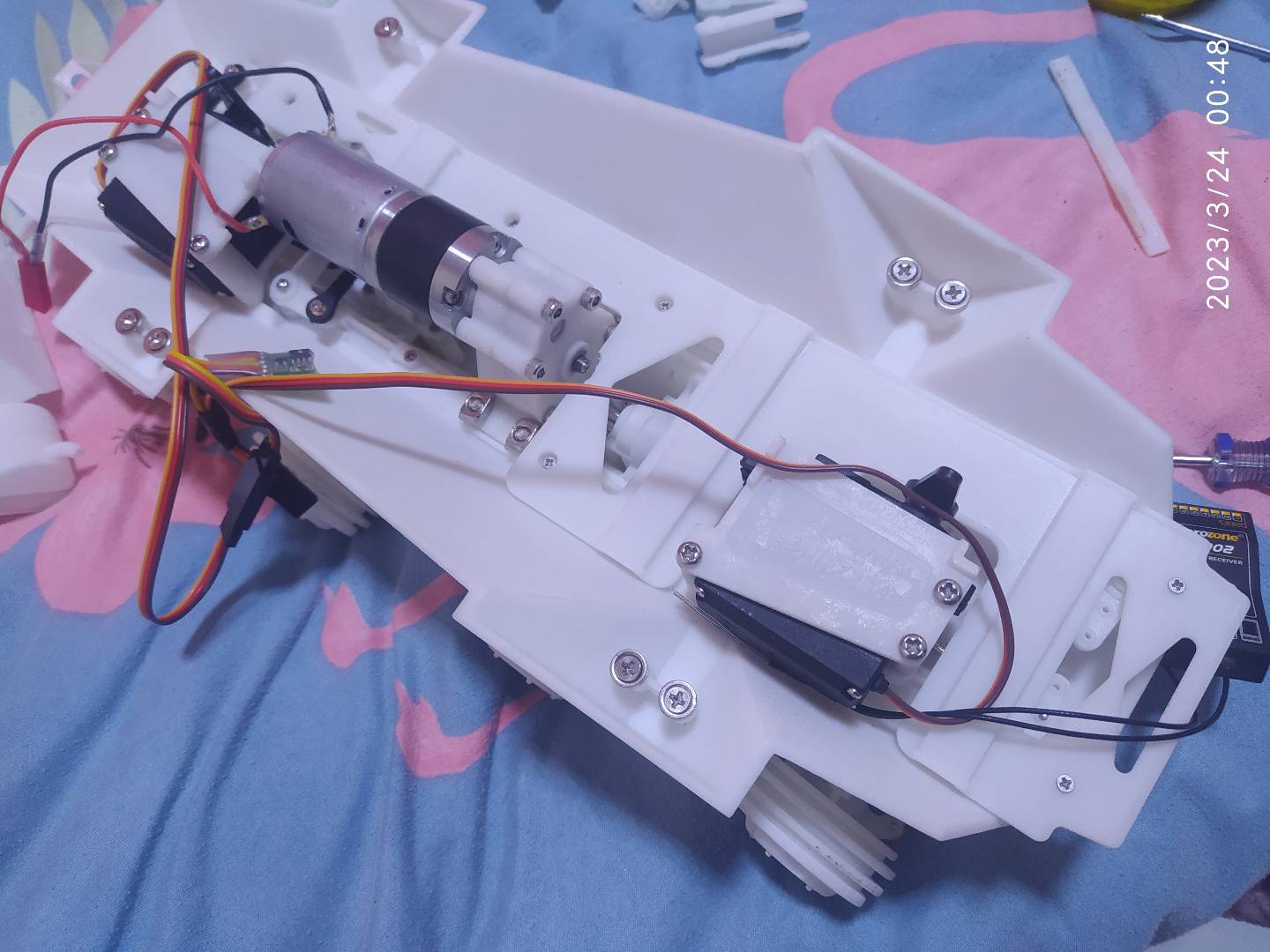
- IMG_20230324_004817.jpg (135.44 KiB) Viewed 1371 times
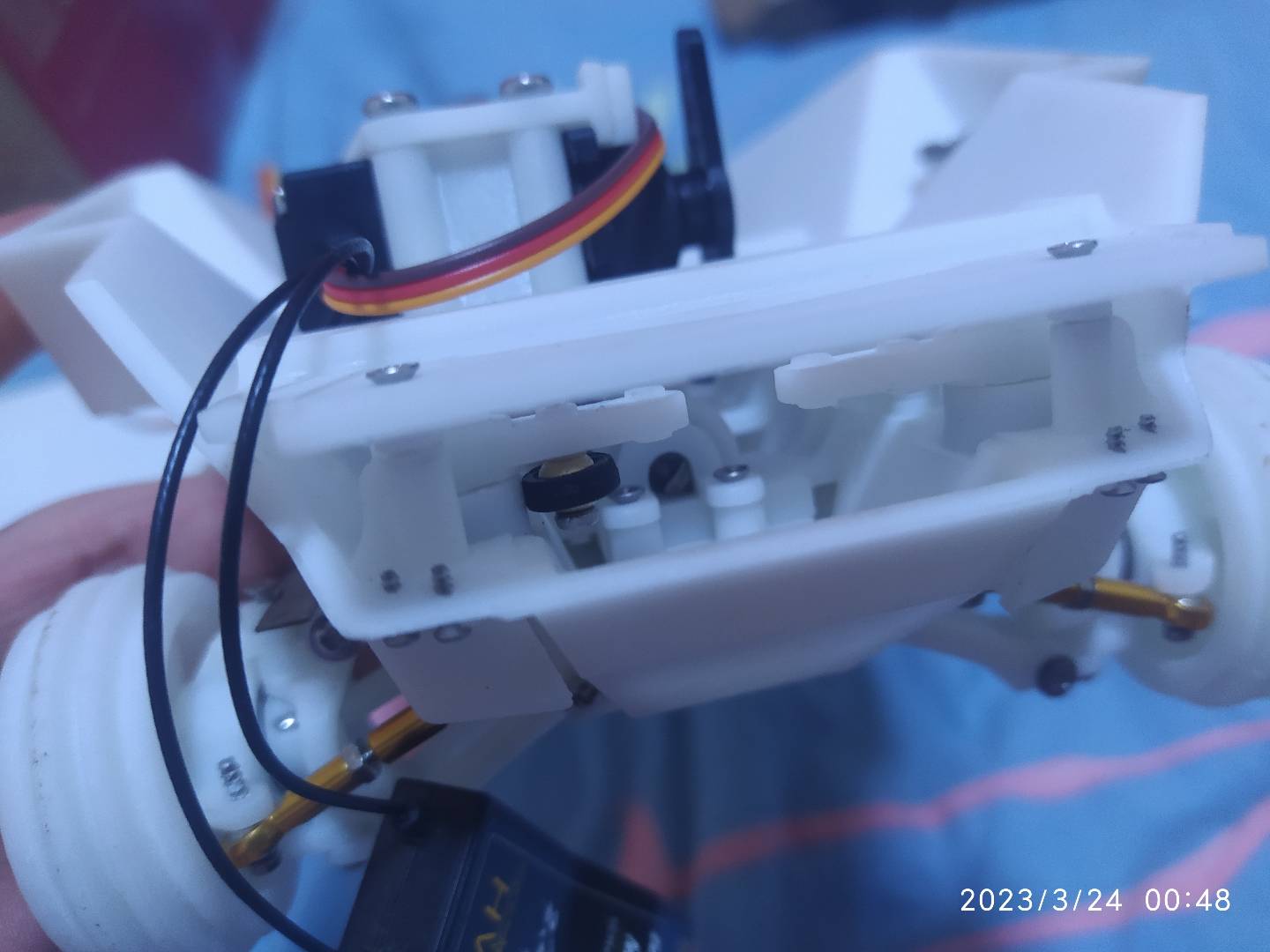
- IMG_20230324_004825.jpg (81.8 KiB) Viewed 1371 times
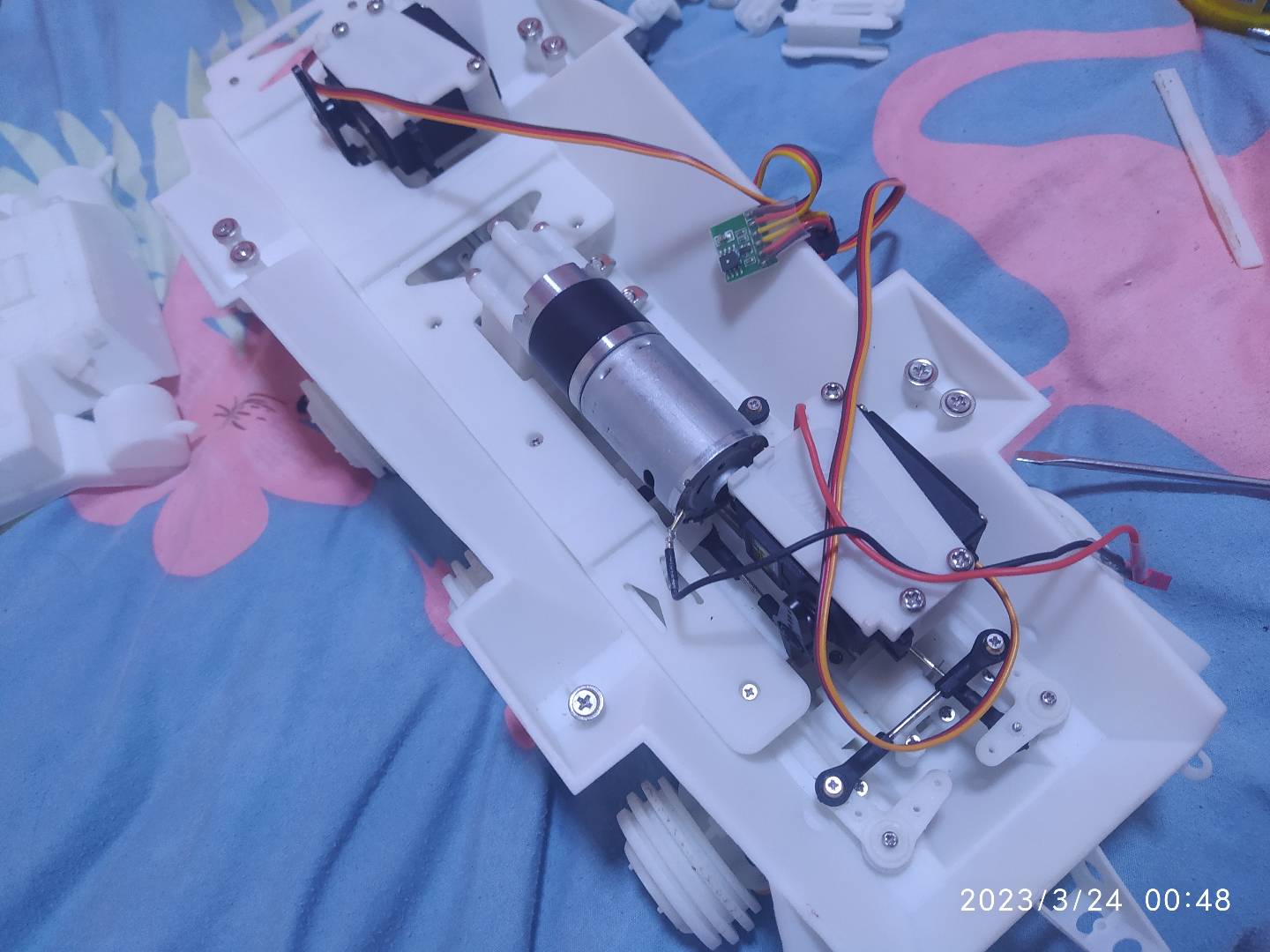
- IMG_20230324_004848.jpg (124.13 KiB) Viewed 1371 times
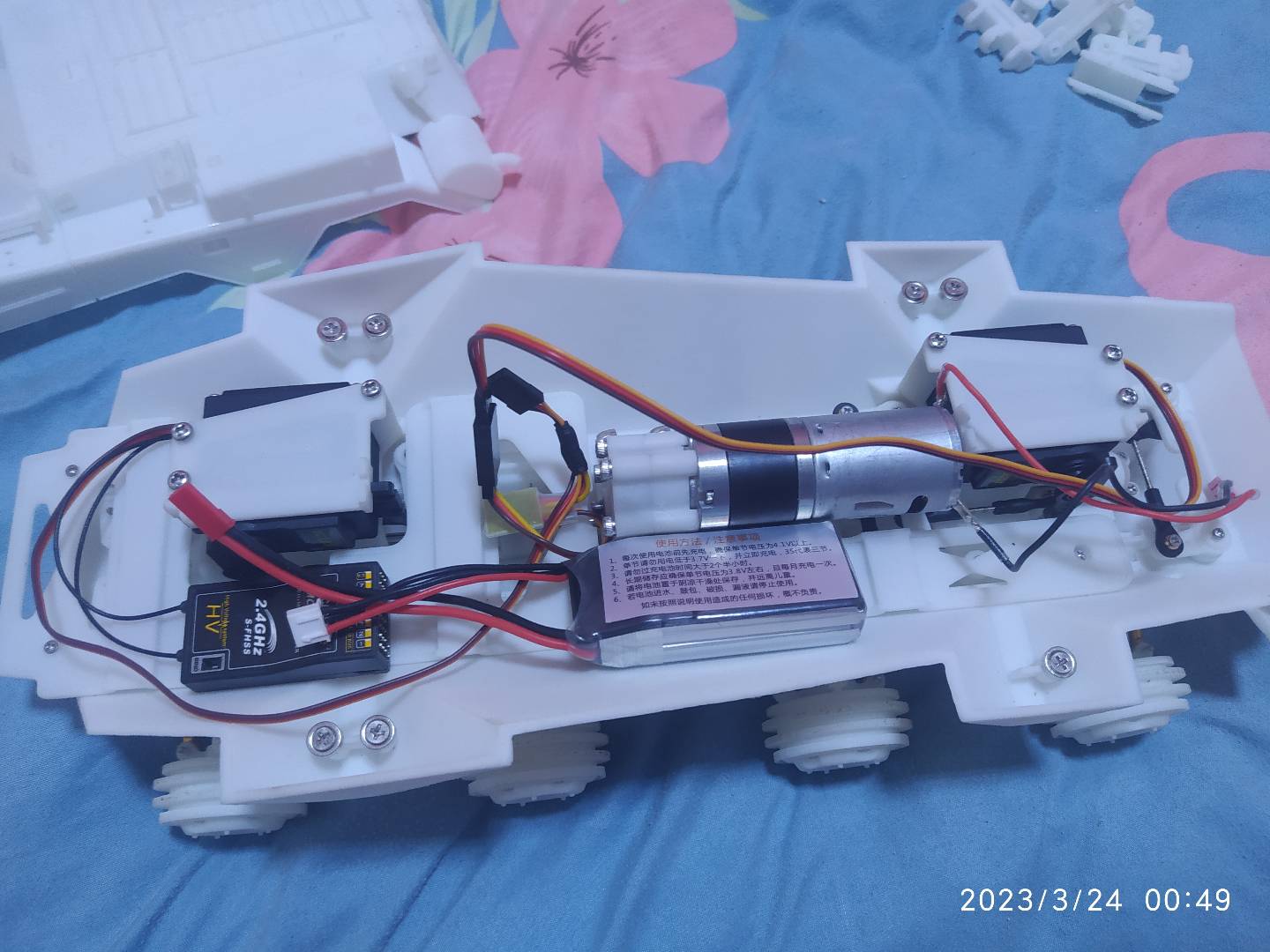
- IMG_20230324_004940.jpg (141.23 KiB) Viewed 1371 times
Due to the fact that the lower part of the chassis of PUMA is too narrow and the middle part is filled with mechanical structures, it is necessary to create a platform on the chassis for fixing electronic equipment.At the same time, the triangular cutout on the platform can fix the wires. Because in my experience, sorting out the wires inside the model is very troublesome.
I powered on and tested that the suspension and steering parts worked well. However, due to the low voltage, the power of the motor is weak, and the driving speed on flat ground is very slow. Therefore, I purchased a new 3S lithium battery, a new electronic governor, and a step-down module. Since the main board can only use 7.2 volts, I first need to connect the electrical regulator and step-down module responsible for the main motor in parallel. This way, the system responsible for advancing has a voltage of 12V, while the rest of the system is still 7.2V